AEM(陰離子交換膜)電解水技術因其潛在的低成本(可使用非貴金屬催化劑)和高靈活性(與波動性可再生能源兼容性好)而受到廣泛關注。其核心組件—膜電極(Membrane Electrode Assembly, MEA)的性能直接決定了電解槽的效率、壽命和成本。制備高性能、高穩定性的膜電極是AEM電解水商業化的關鍵挑戰之一。
核心組件
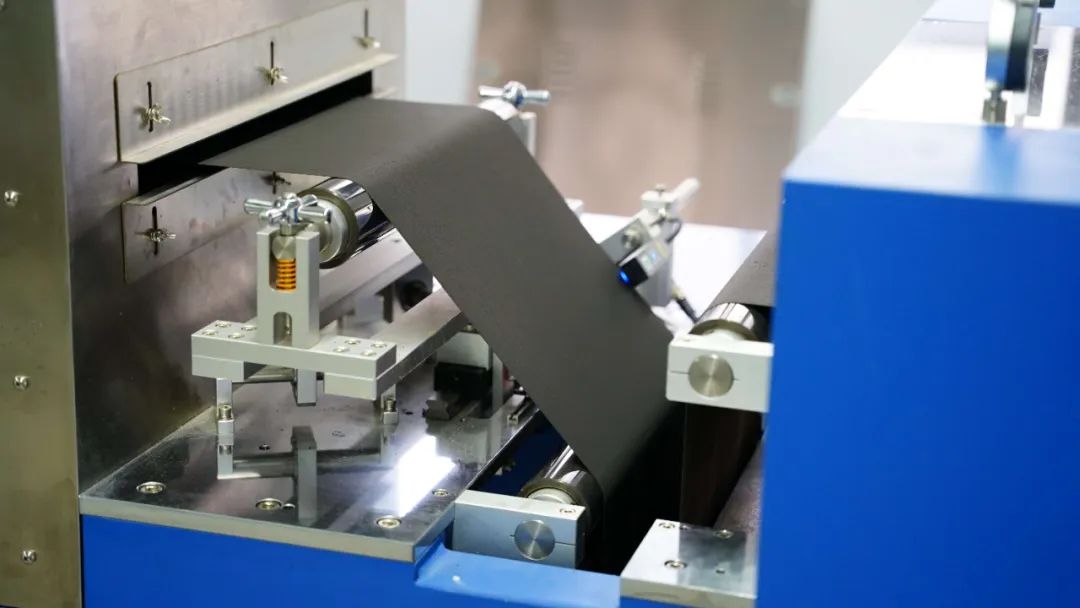
1、陰離子交換膜
傳導氫氧根離子,隔離氫氣和氧氣。
2、催化劑層
陽極(析氧反應,OER):通常使用鎳基(NiFe, NiCo, NiFeCo等)、鈷基(CoOx, CoPx等)或貴金屬(IrO2, RuO2)催化劑。非貴金屬催化劑是AEM的主要優勢之一。
陰極(析氫反應,HER):通常使用鉑族金屬(Pt, Pt/C, PtNi)或非貴金屬(如Ni, NiMo,MoS2,NiMoN)催化劑。
3、氣體擴散層
常為多孔鈦氈、鎳氈、泡沫鎳或碳紙/碳布(需考慮在強堿和高電位下的穩定性)。
作用:導電、傳輸反應物(水)和產物(氣體)、提供機械支撐。
主要制備方法
膜電極的制備核心在于將催化劑層與陰離子膜結合,并確保良好的界面接觸和離子/電子傳導網絡。主要方法分為兩類:
1、催化劑涂層基底法(CCS)
原理:先將催化劑漿料涂覆在氣體擴散層上,形成氣體擴散電極(GDE),然后再將兩側的GDE與陰離子交換膜通過熱壓等方式組裝成MEA。
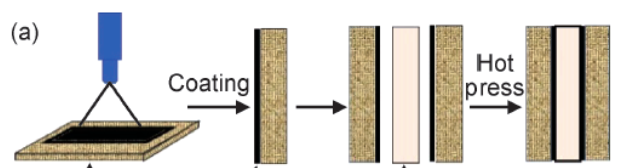
工藝流程:
1)GDE制備
GDE有兩種形式,A)自支撐電極,指材料自身作為電極材料,無需額外的粘結劑、導電劑和集流體,可直接作為電極使用,制備方法主要有電沉積法、水熱原位沉積、刻蝕法、非均相沉積等方法。B)負載型電極,將催化劑漿料涂覆在氣體擴散層上制備的電極。
負載型電極的制備:
催化劑油墨制備:將催化劑粉末(如NiFeOx納米顆粒)、離聚物(陰離子交換聚合物溶液,如季銨化聚芳醚砜、聚苯乙烯乙烯基芐基三甲基氯化銨等)、溶劑(醇/水混合物)混合。通過球磨、超聲、高速剪切等手段充分分散,形成均勻、穩定的漿料(油墨)。離聚物含量和分散均勻性至關重要,它影響催化層內的離子傳導、催化劑利用率和三相反應界面。
涂覆:將油墨涂覆到GDL(鈦氈、鎳氈或處理過的碳材料)上。常用方法為噴涂、刮涂、絲網印刷、浸漬。
2)干燥
在適宜溫度(通常60-80℃)下干燥,去除溶劑。
3)MEA組裝
將陰離子交換膜夾在陽極GDE和陰極GDE之間。
通過熱壓進行組裝:在一定的溫度(通常低于膜的玻璃化轉變溫度或分解溫度,如100-150℃)、壓力(幾MPa到十幾MPa)和時間(幾十秒到幾分鐘)下壓合。熱壓使GDE上的離聚物與AEM表面發生部分融合或緊密接觸,形成良好的離子傳導通道和機械結合。
4)活化/離子交換
組裝好的MEA或單獨的GDE和膜在熱壓前后需要進行離子交換處理(浸泡在KOH中)。
2、催化劑涂層膜法(CCM)
原理:直接將催化劑漿料涂覆在陰離子交換膜的兩側,形成催化劑層。
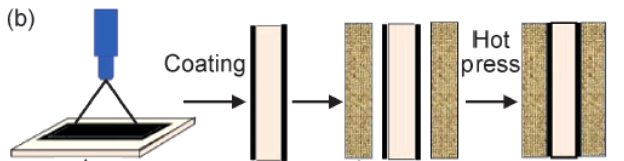
工藝流程:
1)催化劑油墨制備
將催化劑粉末(如NiFeOx納米顆粒)、離聚物(陰離子交換聚合物溶液,如季銨化聚芳醚砜、聚苯乙烯乙烯基芐基三甲基氯化銨等)、溶劑(醇/水混合物,有時加入少量高沸點溶劑如NMP或DMSO)混合。
通過球磨、超聲、高速剪切等手段充分分散,形成均勻、穩定的漿料(油墨)。離聚物含量和分散均勻性至關重要,它影響催化層內的離子傳導、催化劑利用率和三相反應界面。
2)涂覆
噴涂(超聲噴涂、氣動噴涂):該法最常用,可精確控制催化劑載量和均勻性,適合制備薄催化層。將油墨均勻噴涂到AEM膜的兩面。需要控制噴涂參數(壓力、速度、距離、層數、溫度)和膜的狀態(濕度、張力)。
刮涂/刮刀涂布:適合實驗室小批量制備或需要較厚催化層的情況。將油墨倒在膜上,用刮刀控制厚度刮平。
轉印:先將油墨涂在離型膜(如PTFE)上,干燥后再熱壓轉印到AEM上。可避免膜在涂覆過程中溶脹變形。
3)干燥
在適宜溫度(通常60-80℃)下干燥,去除溶劑。需避免溫度過高導致離聚物降解或膜過度收縮。
4)活化/離子交換
將制備好的CCM浸泡在堿性溶液(如KOH)中進行離子交換,使膜和離聚物中的陰離子基團(如Cl-, Br-)轉換為OH-形式。此步驟對提高離子電導率至關重要。
3、混合工藝(CCM+CCS)
如陰極采用CCM(提升膜-催化劑界面接觸),陽極采用CCS(增強穩定性)。
CCM和CCS的優缺點
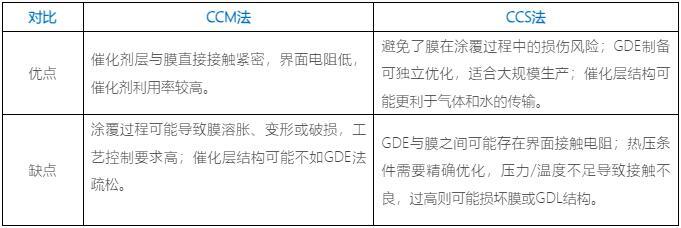
總結
穩石氫能目前采用CCS工藝制備膜電極,產能可達10000m2/年,全電池下,10mA/cm2過電位為117mV,800mA/cm2時電位1.71V,2000h下測試性能衰減低于0.01mV/h。穩石氫能的膜電極性能優異,壽命長,目前已達到商業化應用條件。
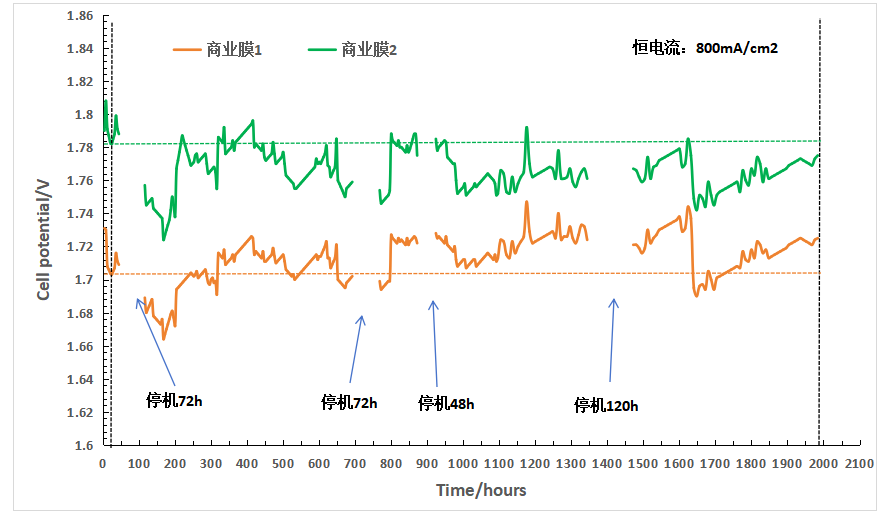
穩石氫能膜電極LSV測試曲線
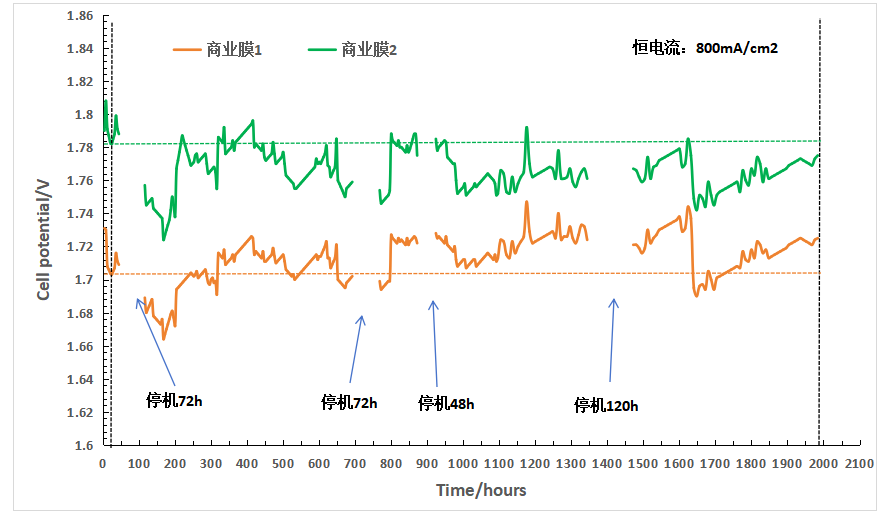
穩石氫能膜電極穩定性測試